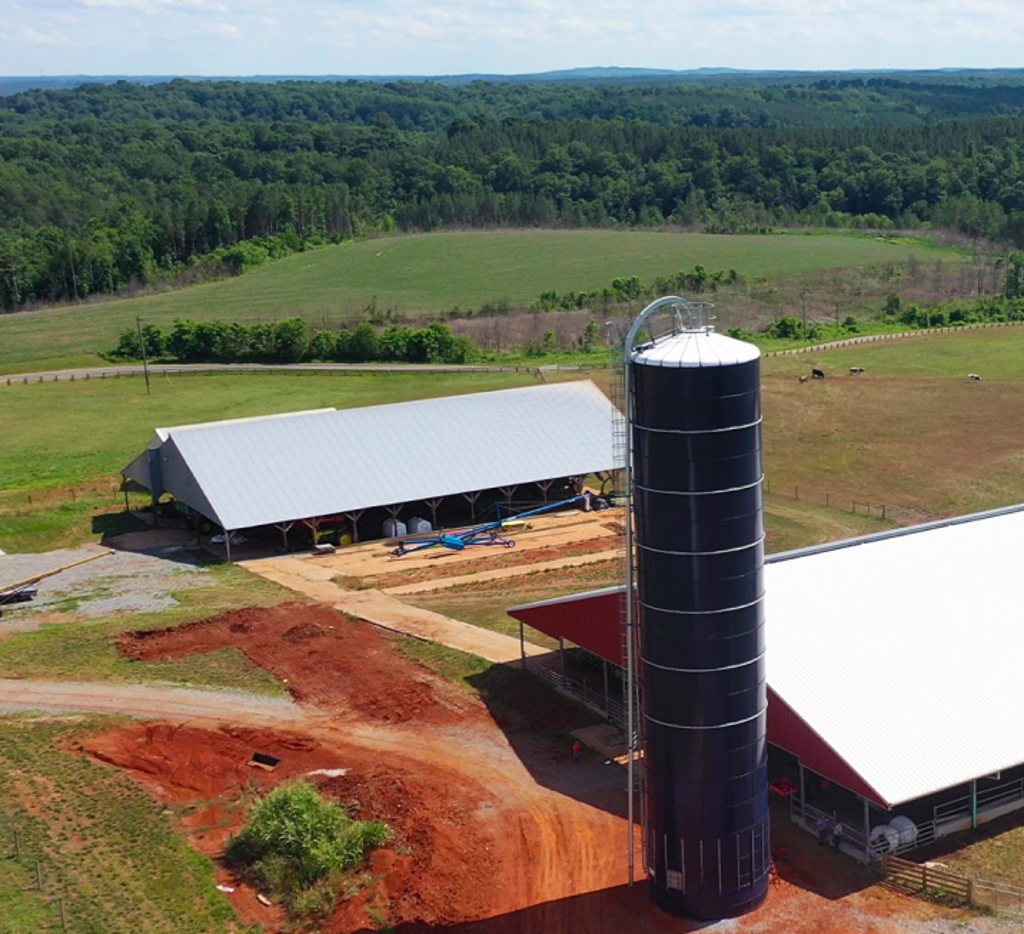
PLANNING AND PREPARING NOW FOR A FUTURE EFFICIENT OPERATION
It’s not often that you meet truly inspirational people, but on one scorching, 98-degree afternoon in June, it happened to this writer. My assignment was to travel about 50 miles from my home to Gladys, Virginia, to interview Myron Yoder, who had just purchased a refurbished Harvestore silo from Greenwood Silo to have installed on his family’s dairy farm. Myron had recently sold his two successful sawmill businesses to purchase the dairy farm that he had grown up on. The most surprising aspect of this story is that Myron Yoder has been totally blind since birth due to a congenital condition.
MEET MYRON YODER
Myron Yoder is a man of many talents and he has overcome many challenges in his life. In this video, he narrates his journey in automating his newly purchased dairy farm in Gladys, Virginia.
After experiencing automation with his sawmill businesses, Myron understood its value and and knew it was a priority. He acknowledged that he had neither the physical ability, nor the inclination, to use the outdated and inefficient bunker and plastic covering method. He was unable to operate the machinery needed to transport stored haylage to the feeding area, and did not want an inefficient system fraught with spoilage, poor feed quality, and toxic runoff problems.
After conducting his own research, Myron spoke to an agricultural nutritionist friend. That conversation led him to Greenwood Silo, and company owner Marvin Reiff. They discussed putting up a refurbished Harvestore silo. “The bag and bunker systems are just a big mess,” Myron said. “I don’t want messes to deal with. I want something that is neat and clean.”
Myron, who had 60 Jersey dairy cows coming in the spring, knew he needed to modernize and automate his operation to accommodate his physical restrictions. The restored and refurbished Harvestore silo is a top-loading, air-sealed silo that’s equipped with the technology Myron needs to feed his cows at the push of a button.

Myron Yoder, Farm Owner
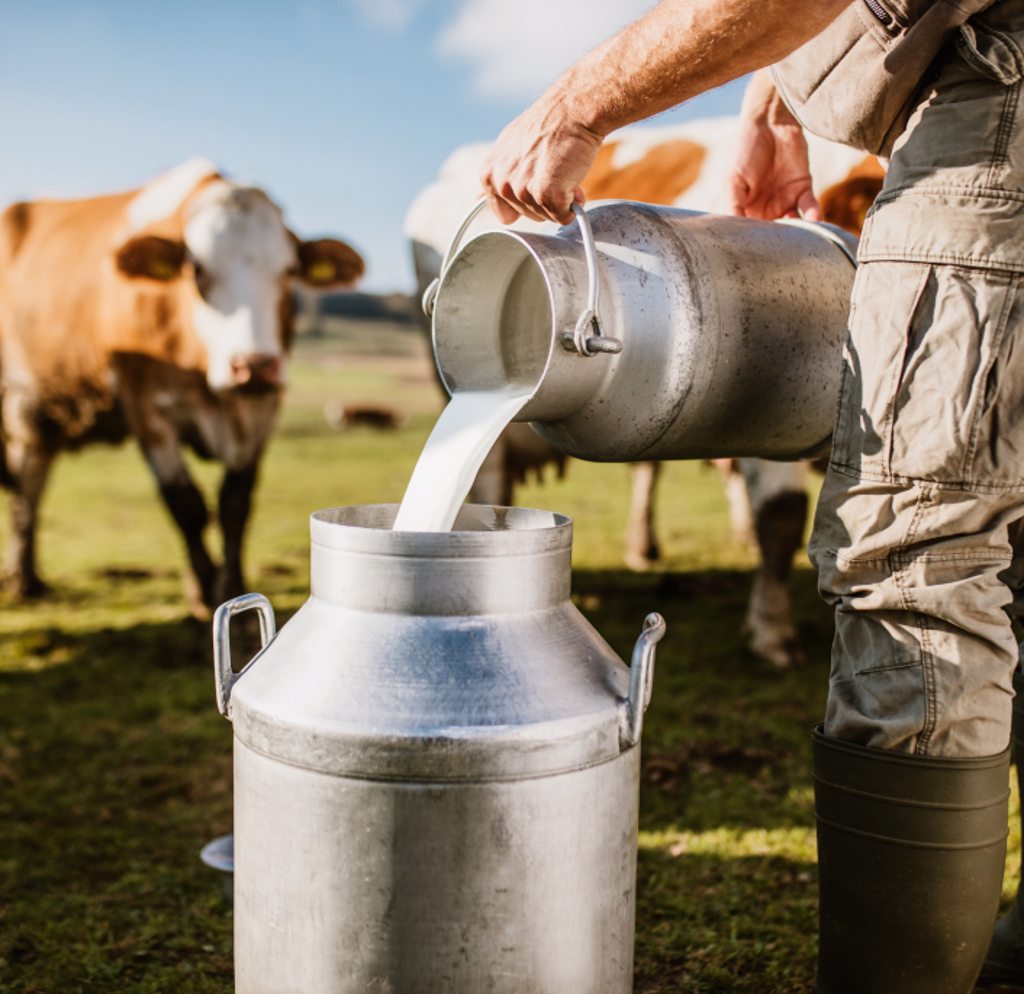
THE SMALL DETAILS OF VERTICAL STORAGE ADD UP
A properly sealed and maintained bottom-unloading silo is a management tool that can benefit your professional farm grazing operation. This vertical storage system renders numerous positive results for your operation and helps achieve a year-round feed supply.
Grazing is good for grass-fed animals. It’s both physically and mentally beneficial for your animals to be outside, get exercise, and eat fresh grass-forages; however, year-round grazing is not a sustainable model due to seasonal weather and growing-season issues.
Here’s why:
- During dry spells, the grass stops growing. This usually leads to animals eating it too close to the ground, stunting regrowth of grasslands.
- When the weather is too wet, animals can easily trample and damage grasslands.
- During the winter, fresh grass isn’t available due to freezing and snow cover.
- In the summer heat, animals can be supplemented with forages from the silo and be fed in the shade, near fans, or during the cool of night.
- A grazing cow has a difficult time getting enough nutritional dry matter due to the fact that unwilted grass-forages can contain more than 80% water in a fresh forage. A finely chopped, wilted forage at a moisture level of 30% to 45% will enable a cow to receive more nutritional dry matter into their system.
- In perfect conditions, grazing animals do not require supplementary feed, but ideal grazing conditions are not permanent.